The 7 Step Guide to Nickel Ore Crusher Maintenance in Indonesia
Selecting the right crusher is only part of the equation for successful nickel ore processing. Effective maintenance and cost optimization strategies are crucial to ensure the longevity of the equipment and to keep operational costs manageable. Here are some key tips to enhance maintenance practices and optimize costs in Indonesian nickel mining operations.
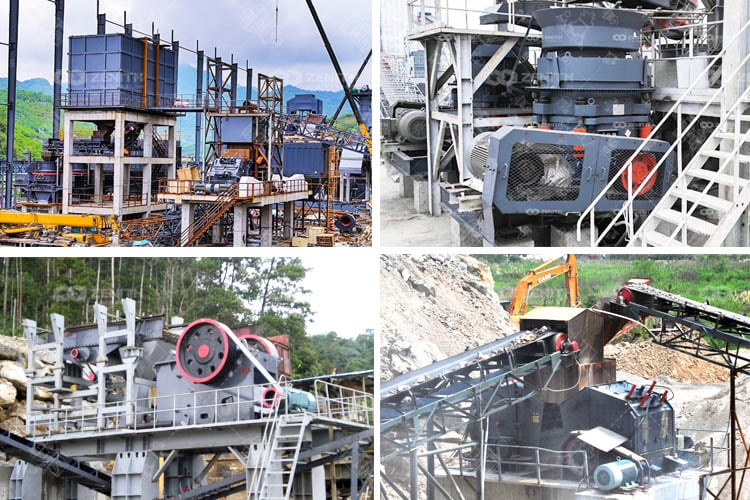
1. Implement a Predictive Maintenance Program
- Regular Inspections: Establish a routine inspection schedule to monitor the condition of critical components such as bearings, liners, and drive systems. Early detection of wear and tear can prevent unexpected breakdowns.
- Condition Monitoring: Utilize condition monitoring technologies (e.g., vibration analysis, thermal imaging) to assess the health of the equipment in real time. This data can help predict failures before they occur, allowing for timely interventions.
2. Optimize Maintenance Practices
- Scheduled Maintenance: Develop a maintenance calendar that aligns with production schedules to minimize downtime. This should include routine tasks such as lubrication, tightening of bolts, and replacement of wear parts.
- Training and Expertise: Ensure that maintenance personnel are well-trained in the specific requirements of nickel ore crushing equipment. Regular training can enhance their skills and improve the effectiveness of maintenance activities.
3. Use Quality Spare Parts
- OEM vs. Aftermarket Parts: Invest in original equipment manufacturer (OEM) parts for critical components. While they may have a higher upfront cost, OEM parts typically offer better performance and durability, leading to lower maintenance costs in the long run.
- Inventory Management: Maintain an inventory of essential spare parts, especially wear components like manganese jaws and ceramic liners. This reduces lead times for repairs and minimizes production downtime due to parts shortages.
4. Optimize Crusher Settings
- Adjustable Settings: Regularly review and adjust the crusher settings based on the material characteristics and production goals. Proper settings can improve the efficiency of the crushing process, reduce wear on the equipment, and lower energy consumption.
- Feed Size Management: Ensure the feed size is within the optimal range for the crusher type. Oversized materials can lead to increased wear and tear, while undersized materials can affect throughput.
5. Energy Efficiency Measures
- Energy Audits: Conduct energy audits to identify areas where energy consumption can be reduced. This may involve optimizing the power supply systems or upgrading to more energy-efficient motors.
- Variable Frequency Drives (VFDs): Implement VFDs on crushers to control motor speed and reduce energy consumption during low-load periods. This can lead to significant savings on energy costs.
6. Enhance Operational Efficiency
- Process Automation: Consider automating certain aspects of the crushing process to improve efficiency and reduce labor costs. Automated systems can optimize feed rates and monitor equipment performance continuously.
- Training Operators: Provide training for operators on best practices for operating crushers, including techniques for managing moisture and sticky materials. Well-trained operators can significantly reduce operational issues and enhance productivity.
7. Monitor and Analyze Performance Metrics
- Key Performance Indicators (KPIs): Establish KPIs to measure the performance of the crushing operation. Metrics such as throughput, downtime, and maintenance costs should be regularly reviewed to identify trends and areas for improvement.
- Data Analysis: Utilize data analytics to assess the performance of the crushing equipment. Analyzing historical data can help identify patterns that lead to inefficiencies, allowing for targeted improvements.
Effective maintenance and cost optimization strategies are essential for maximizing the performance of crushers in Indonesian nickel ore mining. By implementing predictive maintenance programs, optimizing operational practices, and investing in quality parts and training, mining operators can significantly reduce downtime and operational costs. These strategies not only enhance productivity but also contribute to the sustainability of mining operations in Indonesia's challenging environment.