What is the Primary, Secondary and Tertiary Crushing?
In the field of mineral processing, construction, and aggregate production, crushing is a fundamental operation that reduces raw materials into smaller, more manageable sizes. This process is typically divided into three distinct stages: primary, secondary, and tertiary crushing. Each stage serves a specific purpose, utilizing different equipment and techniques to achieve the desired particle size and characteristics. Understanding the differences and applications of each stage is crucial for optimizing production efficiency and product quality.
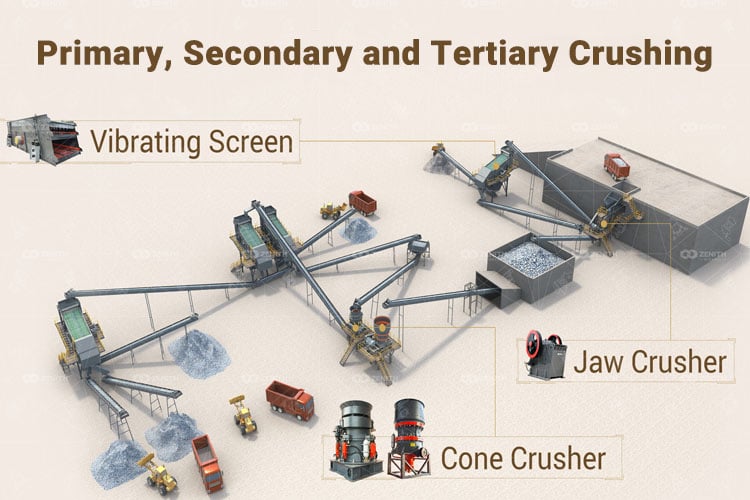
Crushing Process Flow
The crushing process typically begins with the extraction of raw materials from quarries or mines, followed by the crushing stages that reduce the material to the desired size.The crushing process flow can be summarized as follows:
- Extraction: Raw materials are extracted from quarries or mines.
- Primary Crushing: Large rocks are reduced to a manageable size using primary crushers.
- Secondary Crushing: The material is further reduced in size using secondary crushers.
- Tertiary Crushing: The final product is produced through tertiary crushing, achieving the desired size and shape.
The Advantages of Three-Stage Crushing
The crushing process is essential for several reasons:
- Size Reduction: It reduces the size of raw materials, making them easier to handle and process.
- Material Preparation: It prepares materials for subsequent processing stages, such as grinding, screening, and separation.
- Quality Control: It helps achieve specific particle size distributions, which are crucial for the quality of end products.
Primary Crushing
Primary crushing is the first stage of the crushing process, where large rocks are broken down into smaller, more manageable pieces. The primary objective is to reduce the size of the raw material to a size suitable for transportation and further processing. This stage is crucial as it sets the foundation for the subsequent crushing stages.
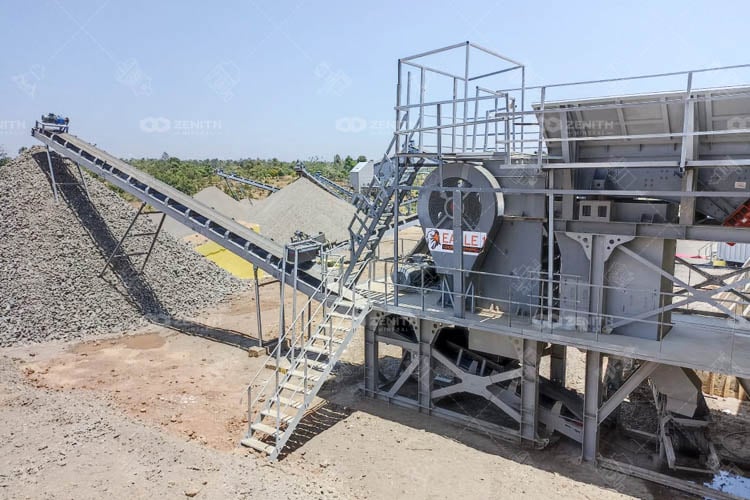
Characteristics of Primary Crushing
- Material Size: Primary crushing typically reduces material sizes to between 4 to 12 inches (100 to 300 mm).
- Throughput: The throughput of primary crushers can vary significantly based on the type of equipment used and the characteristics of the material being processed.
- Product Shape: The shape of the product from primary crushing can vary depending on the type of crusher used. Jaw and gyratory crushers tend to produce more angular particles, while impact crushers can yield more cubical shapes.
Common Equipment Used
The most commonly used equipment for primary crushing includes:Jaw Crushers, Gyratory Crushers and Impact Crushers.
- Jaw Crushers: These machines utilize compressive force to break down materials. They are known for their ability to handle large volumes of material and produce a relatively uniform product size. Jaw crushers are often used in quarries and mining operations.
- Gyratory Crushers: Similar to jaw crushers, gyratory crushers also use compressive force. However, they have a conical shape that allows for a more efficient crushing process. Gyratory crushers are typically used in larger operations where high throughput is required.
- Impact Crushers: These crushers use high-speed impact forces to break down materials. They are suitable for softer materials and can produce a more cubical product shape.
Secondary Crushing
Secondary crushing follows primary crushing and aims to further reduce the size of the material produced in the first stage. The primary goal is to achieve a specific particle size distribution suitable for downstream processing, such as screening or tertiary crushing.
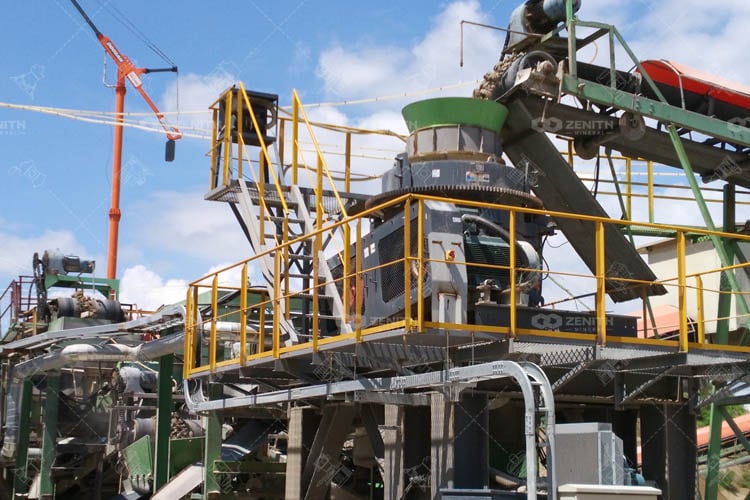
Characteristics of Secondary Crushing
- Material Size: Secondary crushing typically reduces material sizes to between 1 to 4 inches (25 to 100 mm).
- Throughput: Secondary crushers generally have a higher throughput than primary crushers, allowing for increased efficiency in the crushing process.
- Product Shape: The product shape from secondary crushing is often more uniform and consistent, improving the quality of the final product.
Common Equipment Used
The equipment commonly used for secondary crushing includes:Cone Crushers,Horizontal Shaft Impact (HSI) Crushers,Vertical Shaft Impact (VSI) Crushers.
- Cone Crushers: These crushers are designed to crush materials between a moving cone and a fixed outer cone. Cone crushers are highly efficient and can produce a finely crushed product with a consistent size.
- Horizontal Shaft Impact (HSI) Crushers: HSI crushers use high-speed impact to break down materials. They are effective for producing a wide range of particle sizes and shapes.
- Vertical Shaft Impact (VSI) Crushers: VSI crushers are used to produce high-quality, cubical aggregates. They utilize a high-speed rotor to fling material against a hard surface, creating a unique crushing action.
Tertiary Crushing
Tertiary crushing is the final stage in the crushing process, focusing on producing a specific particle size and shape for end-use applications. This stage is crucial for achieving the desired specifications for construction aggregates, asphalt, and concrete.
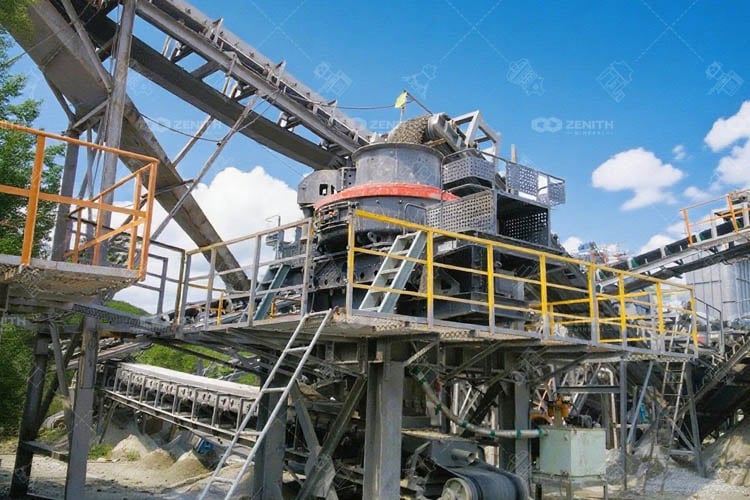
Characteristics of Tertiary Crushing
- Material Size: Tertiary crushing typically reduces material sizes to less than 1 inch (25 mm).
- Throughput: Tertiary crushers usually have a lower throughput compared to primary and secondary crushers, as they focus on producing a specific product size and quality.
- Product Shape: The final product from tertiary crushing is often highly uniform and cubical, meeting the specifications required for various applications.
Common Equipment Used
The equipment commonly used for tertiary crushing includes:
- Cone Crushers: Tertiary cone crushers are often used to produce finely crushed material. They can achieve a high reduction ratio and produce a well-graded product.
- Vertical Shaft Impact (VSI) Crushers: In addition to their use in secondary crushing, VSI crushers are also effective in tertiary applications, producing high-quality, cubical aggregates.
- Roll Crushers: These crushers use two rotating rolls to crush the material. They are effective for producing a uniform product size and can handle a variety of materials.
Importance of Each Crushing Stage
Each stage of the crushing process plays a vital role in ensuring the efficiency and effectiveness of material processing. The importance of each stage can be summarized as follows:
- Primary Crushing: Establishes the foundation for the entire crushing process by breaking down large rocks into manageable sizes.
- Secondary Crushing: Further refines the material, ensuring that it meets the required specifications for downstream processing.
- Tertiary Crushing: Produces the final product, focusing on achieving specific particle sizes and shapes necessary for various applications.
Understanding the stages of crushing—primary, secondary, and tertiary—is essential for professionals in the mining, construction, and recycling industries. Each stage serves a distinct purpose and utilizes different types of equipment to achieve specific particle sizes and shapes. By optimizing the crushing process, companies can enhance efficiency, reduce costs, and ensure the production of high-quality materials for their projects.